Experten-Blog
Eisglätte und Gewitter in der Instandhaltung?
Der Autor Yuval Noah Harari beschreibt in seinem Buch Eine kurze Geschichte der Menschheit die Entwicklung der Menschen bis zum „Beherrscher der Erde“ - eine, im Vergleich zur Existenz unseres Universums, relativ kurze Zeitspanne von knapp 70.000 Jahren. An einer Stelle geht er dabei auch auf Prognose-Systeme ein. Dabei handelt es sich um Anwendungen, die uns Menschen frühzeitig vor Änderungen oder Gefahren warnen sollen. Ein Beispiel für solch ein Prognose-System, das jeder kennt, ist der Wetterbericht. Wettervorhersagen sollen uns vor Stürmen, Gewittern, Eisglätte und ähnlichen natürlichen Phänomenen warnen. Eine gute Sache, sollte man meinen…
Tatsächlich stellt uns die Vorhersage des Wetters vor ein Dilemma: Zwar wissen wir durch regelmäßige Beobachtung des Wettergeschehens, wie das Wetter morgen oder kommende Woche wahrscheinlich wird. Doch trotz bereits Jahrhunderte andauernder wissenschaftlicher Forschung können wir nichts gegen das Wetter und seine Auswirkungen tun.
Gilt das auch für die Instandhaltung? Nein!
In der Industrie bauen einzelne Produktionsschritte perfekt abgestimmt aufeinander auf und setzen die Funktionsfähigkeit aller benötigten Produktionsanlagen voraus. Versagen diese an einer Stelle, steht schlimmstenfalls das gesamte System still. Um dies zu verhindern, müssen Maschinen in Stand gehalten werden. Wenn wir von „Instandhaltung“ sprechen, unterscheiden wir vier klassische Bereiche:
1. Wartung: den „Soll-Zustand“ bewahren
2. Inspektion: den „Ist-Zustand“ feststellen
3. Instandsetzung: Reparaturen vornehmen
4. Verbesserung: Schwachstellen beseitigen.
Die beste Instandhaltungsstrategie ist eine, die Ausfälle von Produktionsanlagen aktiv verhindert und Produktionsabläufe am wenigsten stört, d.h. Maßnahmen in Zeiten einplant, in denen die Anlage ohnehin stillsteht, also kaum wahrgenommen wird. Dazu benötigt die Instandhaltung Informationen über den aktuellen und zu erwartenden Zustand von Produktionsanlagen.
Und genau hier liegt ein Dilemma: Zunehmende Ausstattung mit Sensorik, viele Daten und Analysen liefern umfassende Informationen zum Betrieb und Zustand technischer Anlagen. Der Einsatz KI-gestützter Werkzeuge ermöglicht es, kritische Betriebszustände und potenzielle Störungen, z.B. durch Schäden an Wälzlagern oder Leckagen an Wärmetauschern, rechtzeitig zu erkennen und die Ursachen zu identifizieren. Die Instandhaltung verfügt damit über ausreichende Informationen, um technisch bedingte Störungen an Produktionsanlagen verhindern zu können. Es kommt nun darauf an, diese richtig zu nutzen.
In der betrieblichen Praxis zeigt sich aber, dass es immer noch zu viele Störungen gibt. Anlagen werden nach einem Ausfall mit dem Ziel einer schnellen Wiederinbetriebnahme instandgesetzt. Wartungsmaßnahmen werden aufgeschoben und statt Schwachstellen systematisch zu beseitigen, werden oftmals lediglich Symptome bearbeitet, ohne die Ursachen von Störungen zu beseitigen. Anders gesagt heißt das: Betreiber nutzen das Potenzial einer datengestützten Instandhaltung in Verbindung mit Prognosen potenzieller Störungen bisher unzureichend. In Verbindung mit einer falschen Beschaffungsstrategie, d.h. möglichst bei den Investitionskosten zu Lasten der späteren Betriebs- und Instandhaltungskosten zu sparen, gehen Unternehmen eine risikoreiche Wette ein, dass eine Anlage über einen langen Betriebszeitraum zuverlässig und kostengünstig funktioniert.
Wir vom Team des Themenclusters „Instandhaltungsfreie Produktions- und Logistiksysteme“ des Innovationsprogramms RESYST haben es uns zur Aufgabe gemacht, die beschriebene Situation zu verbessern. Dazu entwickeln wir Methoden zur Beschreibung und Einordnung von Stressfaktoren auf technische Anlagen, zur Risiko- und Resilienzbewertung sowie zur Ableitung resilienzerhöhender Maßnahmen in Produktionsanlagen weiter. Das alles ist eng verbunden mit der Entwicklung neuer Werkzeuge zur Zustandsüberwachung und zu erklärbaren Lebensdauerprognosen, Instandhaltungsplanung bis hin zu Kompetenzprofilen von Mitarbeitenden für eine zukunftssichere Instandhaltung.
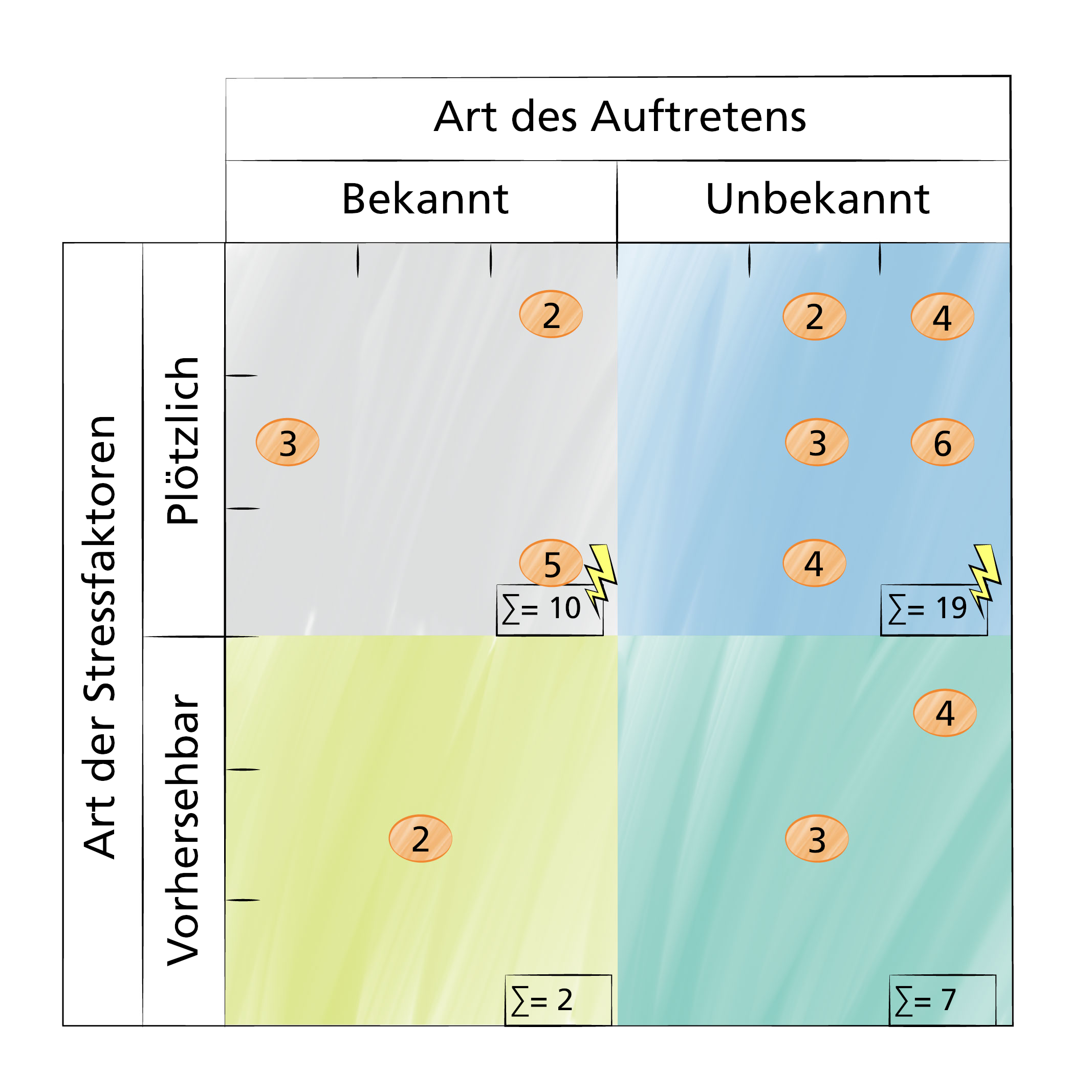
Mein persönliches Herzensanliegen ist es, die Instandhaltung oder besser das Anlagenmanagement als gemeinschaftliche Aufgabe u.a. der Bereiche Produktentwicklung, Produktion, Produktionsplanung und –steuerung, Instandhaltung, Qualitätssicherung, Sicherheits-, Gesundheits- und Umweltschutz und Logistik unter Einbeziehung externer Dienstleister im Unternehmen zu etablieren. Gleichzeitig muss sich an der Zusammenarbeit zwischen Anlagenherstellern und Anlagenbetreibern grundsätzlich etwas ändern.
Betreiber müssen gegenüber Herstellern honorieren, dass Qualität - hier im Sinne einer nachgewiesenen Zuverlässigkeit und Resilienz – ihren Preis hat, ebenso die Erfassung und Bereitstellung von Daten und Analysen aus den Anlagen.
Hersteller müssen auf der Grundlage ihres detaillierten Wissens über den Aufbau und die Funktionen ihrer Produkte mehr auf die tatsächlichen Bedürfnisse ihrer Auftraggeber eingehen, ihre Produkte entsprechend gestalten und individuell angepasste Serviceangebote unterbreiten.
Beide Seiten müssen letztlich davon überzeugt sein, dass die darin enthaltenen Maßnahmen im Sinne der Zuverlässigkeit von Anlagen technisch erforderlich und wirtschaftlich vertretbar sind.
An dieser Stelle möchte ich noch einmal das Eingangs-Statement bezüglich der Bedeutung von Prognosen zum Ausfallverhalten technischer Anlagen aufgreifen. An Werkzeugen dafür mangelt es uns nicht. Nutzen wir sie richtig und konsequent! Sie sind die Grundlage, um die Idee einer instandhaltungsfreien Produktion schrittweise wahr werden zu lassen.
Ihr Frank Ryll